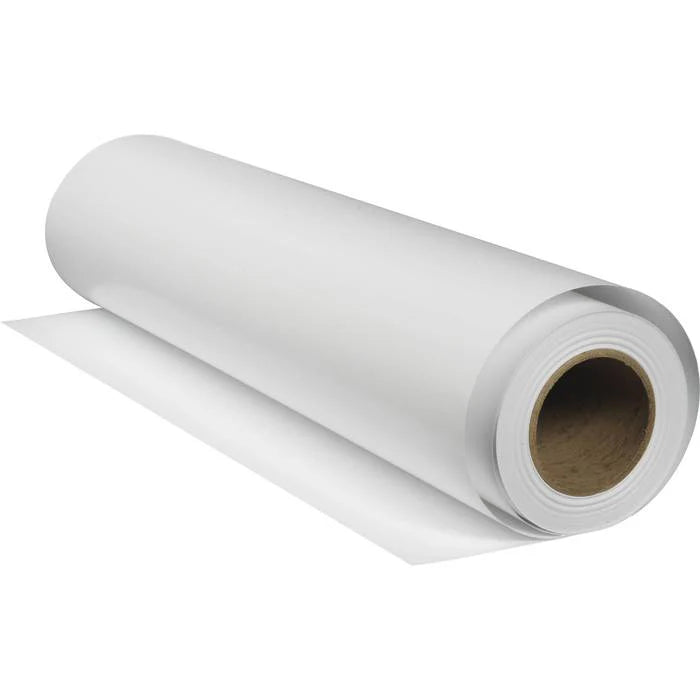
Say Goodbye to Thick Transfers: Upgrade to Our Top-Quality DTF Materials
Share
The thickness of Direct-to-Film (DTF) prints can vary due to several factors, including the type of ink used, the quality of the film, the printer settings, and the curing process. Here’s a breakdown of why some DTF prints appear thick while others are thin:
1. Ink Type and Quality
- Pigment-based vs. Dye-based Inks: Pigment-based inks tend to create more vibrant, thicker prints compared to dye-based inks. This is because pigment particles are larger and sit more prominently on the film, leading to a thicker layer of ink.
- Ink Viscosity: Thicker inks can result in more ink being deposited on the film. If the ink is too thick or not optimized for DTF printing, it can cause a heavier print. On the other hand, thinner inks or those that are better formulated for DTF processes tend to result in more delicate, thinner prints.
2. Film Type
- The type of film used for DTF printing can impact the print thickness. Some films are more porous and absorb more ink, leading to thinner prints, while others are designed to keep ink on the surface, resulting in thicker prints.
- Films with different coatings (matte, glossy, or satin) can also affect how the ink adheres and spreads, influencing the print's final appearance.
3. Printer Settings
- Print Density: Printer settings, like the print density or saturation, can determine how much ink is deposited on the film. Higher density settings lead to more ink being used, which results in a thicker print.
- Passes and Resolution: Some printers allow you to adjust the number of passes (how many times the print head goes over the area). More passes can increase the thickness of the ink layer, as more ink is applied per pass. Additionally, high-resolution settings may deposit finer ink layers, creating thinner prints.
4. Curing Process
- Curing Temperature and Time: After printing, the ink is typically cured with heat. The curing process affects how the ink dries and hardens on the film. If the curing process is too short or the temperature is too low, the ink may not fully adhere or cure, leading to a thinner and possibly more prone to smudging print. Over-curing can sometimes cause the ink to become overly thick or cracked.
- Curing Equipment: The type of heat press or oven used can also affect how thick the final print is. Different curing devices and settings can result in variations in how the ink bonds to the film, influencing the final thickness.
5. Transfer Powder
- DTF printing uses adhesive powder to help bond the ink to the fabric during the transfer process. If too much powder is applied, it can create a thicker coating, and the print will appear more pronounced or “heavier.” On the other hand, insufficient powder can make the transfer weaker or less defined, leading to a thinner print.
6. Printer Maintenance
- Nozzle Clogs and Ink Flow: If the printer's nozzles are partially clogged or if the ink isn’t flowing properly, it may not deposit ink evenly or sufficiently. This can result in inconsistent print thickness, with some areas appearing thicker or more saturated than others.
7. Film and Transfer Layer Thickness
- The print quality also depends on the thickness of the transfer film and adhesive layer. A thicker transfer film may result in a more robust print that stands out, while a thinner film might make the design appear more delicate.
At DTF Parts store we offer only the best quality supplies to ensure that you get the most consistent, high-quality results. If you’ve noticed that your transfers feel a bit thick or heavy, it might be time to try out our premium inks, films, and powders. Our products are specifically designed to deliver a smoother, more refined finish with the perfect balance of thickness—ideal for achieving the most vibrant, professional-looking DTF prints. Give our supplies a try and experience the difference for yourself!